Cosa si intende per Revamping e Retrofit in azienda
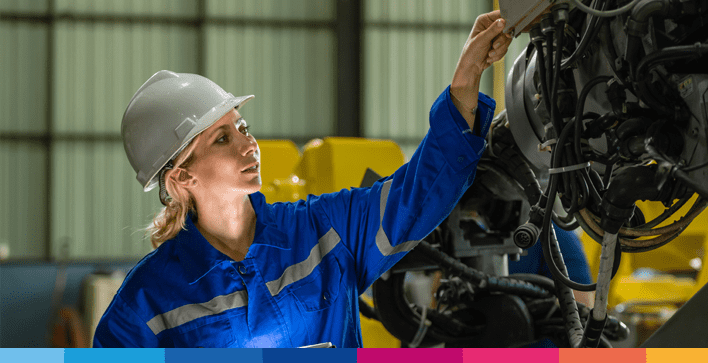
Revamping e Retrofit rappresentano strategie vitali per le aziende che mirano a ottimizzare le operazioni e rimanere competitive. Scopriamo insieme come queste pratiche migliorano l’efficienza operativa, riducendo i costi.
La situazione italiana
L’età media dei macchinari industriali italiani è molto alta. I dati parlano di parchi macchine che in media hanno 14 anni e 5 mesi. Riuscire ad integrarli con le nuove soluzioni tecnologiche non è semplice. Le strade che le aziende manifatturiere possono intraprendere sono tre: comprare un nuovo macchinario, fare revamping o scegliere una soluzione retrofit.
Perché i macchinari industriali invecchiano?
A rendere obsoleti i macchinari nel tempo sono principalmente due fattori.
Il primo è la parte hardware. La nascita di nuovi sistemi di connessione (si pensi al passaggio dalle porte seriali di tipo RS a quelle Ethernet) rende necessario aggiornare le entrate dei macchinari per poterli connettere alle nuove soluzioni di Industria 5.0.
Il secondo fattore, invece, riguarda il software. Molto spesso i fornitori non ci sono più o non è possibile aggiornare il software perché per farlo è necessario un sistema informativo ormai non più utilizzato. Ad esempio, per programmare un software di 20 anni fa, servirebbe un computer con un sistema operativo di quel periodo, dispositivo ormai non più presente e utilizzato dalle aziende.
Comprare un nuovo macchinario potrebbe sembrare la strada più veloce e semplice. A livello economico, però, spesso non è sostenibile. Inoltre, talvolta i macchinari, benché obsoleti, sono performanti e per questo cambiarli non è la decisione migliore da intraprendere. La soluzione può quindi essere una tra revamping o retrofit dei macchinari.
Revamping: cos’è e quali sono i rischi
Con revamping si indica l’ammodernamento di un sistema già utilizzato. Il termine viene dal mondo ferroviario, con cui ad esempio si indicava la possibilità di installare un sistema di aria condizionata in un vagone treno che prima ne era sprovvisto.
Applicato al mondo manifatturiero, con revamping si indica il processo con cui si ricostruisce l’intera componente elettrica di un macchinario: un intervento rischioso, perché non si può essere sicuri del corretto funzionamento finale, costoso e lungo.
L’azienda, inoltre, deve investire lato software e individuare la soluzione migliore che possa essere aggiornata con il passare del tempo.
Retrofit: cos’è e perché conviene
I costi legati all’acquisto di un nuovo macchinario e i rischi connessi al revamping portano sempre più aziende a scegliere la strada del retrofit.
Con retrofit si indica una soluzione che è in grado di comunicare con un macchinario, estraendo e inviando dati, qualunque siano il suo software o le entrate hardware.
Rappresenta quindi la soluzione ideale per digitalizzare macchinari ancora performanti e funzionanti, tramite un investimento limitato e con un ritorno veloce e sicuro.
Prediligere questo approccio, inoltre, consente con una sola soluzione di collegare tra di loro tutti i macchinari di uno stabilimento. Nuovi oppure obsoleti, di produttori diversi e con software differenti, non ha importanza. L’approccio retrofit consente di estrarre dati omogenei da qualsiasi macchinario e avere così una vera e propria fabbrica interconnessa e digitalizzata.
Retrofit elettrico: una scelta sostenibile
Il retrofit elettrico emerge come strategia fondamentale per promuovere la sostenibilità energetica. Questo processo consiste nell’aggiornare impianti e sistemi esistenti con tecnologie più efficienti e a minor impatto ambientale. Attraverso l’aggiornamento di apparecchiature elettriche, sistemi di illuminazione e quadri elettrici, si mira a ridurre i consumi energetici, ottimizzare l’efficienza e risparmiare sui costi operativi. Il retrofit elettrico rappresenta quindi un passo significativo verso un’economia più verde e responsabile.
La soluzione retrofit di TeamSystem
Il software MES di TeamSystem, grazie al fatto di essere Plug&Play e in Cloud, consente di estrarre dati da qualsiasi macchinario. Si collega, infatti, nel quadro elettrico del macchinario e, tramite dei sensori, è in grado di estrarre i dati produttivi (ad esempio i pezzi prodotti, gli scarti, la temperatura, etc).
Un approccio veloce, sicuro e accessibile, che consente anche alle piccole-medio aziende manifatturiere di compiere il loro primo passo verso una fabbrica connessa e digitale.
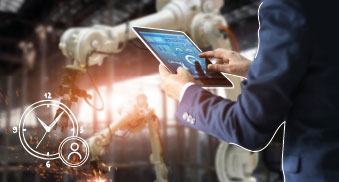