Ottimizzazione dei processi produttivi, tra AI e IoT
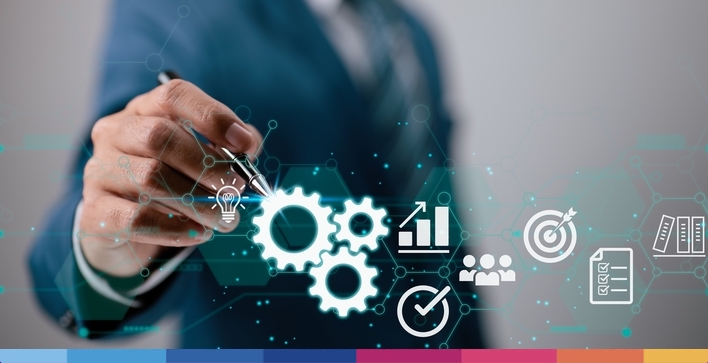
Parlare di ottimizzazione dei processi produttivi oggi significa affacciarsi a quella che è ormai riconosciuta come una vera e propria rivoluzione. In particolare, l’industria manifatturiera, tradizionalmente caratterizzata dalla produzione di beni mediante processi meccanici e manuali, sta attraversando cambiamenti radicali e dal fortissimo impatto in una moltitudine di settori.
Oggi parliamo ormai di Industria 4.0 e di Smart Factory, in cui le fabbriche non sono più semplici luoghi di produzione, ma veri e propri ecosistemi tecnologici intelligenti. Una rivoluzione sostenuta da due tecnologie di cui si sente parlare sempre più spesso: ci riferiamo all’intelligenza artificiale e all’Internet of Things, la cui introduzione nei processi produttivi ha aperto le porte a una maggiore efficienza, alla riduzione dei costi operativi e al miglioramento della qualità dei prodotti.
Un’innovazione di questo tipo non può che comportare anche delle sfide significative. L’Industria 4.0, infatti, non richiede solo di implementare tecnologie all’avanguardia, ma implica anche una profonda trasformazione culturale e organizzativa. L’accettazione da parte dell’uomo è fondamentale: l’obiettivo non è sostituire il lavoro umano, bensì potenziarlo attraverso la collaborazione sinergica con le nuove tecnologie.
Non solo, bisogna ricordare anche che la rivoluzione industriale non riguarda solo le grandi aziende. Negli ultimi anni, sempre più PMI in Italia stanno abbracciando le nuove tecnologie, migliorando i processi produttivi e abbracciando la transizione verso l’industria 4.0, anche grazie a strumenti nati per semplificarla.
Ne parliamo in questa guida.
IoT e AI: cosa sono e come funzionano
In un mercato sempre più dinamico ed esigente, le aziende hanno trovato nell’implementazione delle nuove tecnologie nei propri processi produttivi il modo per restare competitive, aumentando l’efficienza e la redditività.
In particolare, l’intelligenza artificiale (AI) e l’Internet of Things (IoT) rappresentano i pilastri della trasformazione digitale nell’industria manifatturiera.
Intelligenza Artificiale (AI)
Quando parliamo di AI facciamo riferimento a sistemi informatici che, proprio come gli esseri umani, percepiscono l’ambiente circostante, imparano nuove informazioni, prendono decisioni basate su esperienze passate, intraprendono azioni e migliorano le proprie capacità nel tempo.
Solo per fare degli esempi, in campo manifatturiero l’AI può aumentare l’efficienza dei processi produttivi tramite:
- analisi predittive avanzate, ottimizzando anche la manutenzione predittiva;
- analisi dei dati operativi in tempo reale, riducendo gli sprechi e ottimizzando le risorse;
- personalizzazione della produzione, permettendo un adattamento dinamico alle richieste del mercato.
Internet of Things (IoT)
D’altra parte, l’IoT fornisce un monitoraggio dettagliato e una connessione diretta tra dispositivi. Acronimo di Internet of Things (Internet delle cose), l’IoT fa riferimento al concetto in cui oggetti fisici, come dispositivi elettronici, veicoli, elettrodomestici ecc., sono dotati di sensori, software e connessioni di rete, permettendo loro di raccogliere e scambiare dati.
Ciò consente la creazione di un ambiente interconnesso in cui i dati vengono raccolti, condivisi e utilizzati con l’obiettivo di migliorare l’efficienza produttiva.
In particolare, l’Internet of Things permette di migliorare i processi produttivi tramite:
- raccolta di dati in tempo reale, fornendo dati immediati sullo stato delle attrezzature e dei processi produttivi.;
- manutenzione preventiva, grazie alla raccolta e analisi sulla salute delle macchine e delle attrezzature;
- controllo automatizzato dei sistemi energetici, riducendo gli sprechi e ottimizzando l’efficienza energetica complessiva della produzione.
Come AI e IoT rivoluzionano i processi produttivi
Abbiamo già visto, in parte, come le nuove tecnologie contribuiscono ad aumentare l’efficienza dei processi produttivi.
La possibilità di anticipare guasti, ottimizzare la produzione in tempo reale e implementare pratiche di manutenzione preventiva, però, sono solo alcune delle ragioni per cui l’adozione di AI e IoT è diventata imprescindibile.
Infatti sono diversi i motivi per cui queste tecnologie stanno rivoluzionando i processi produttivi nel settore manifatturiero.
Analizziamo a seguire i punti principali in modo più approfondito.
1. Automazione dei processi produttivi
L’automazione intelligente sta rivoluzionando i processi produttivi introducendo un livello avanzato di autonomia e intelligenza nelle operazioni industriali.
Grazie a tecnologie come AI, IoT e Machine Learning è possibile integrare sistemi di controllo e decisionali che possono apprendere dai dati, prendere decisioni autonome e adattarsi dinamicamente alle variazioni delle condizioni di produzione.
Il risultato è il raggiungimento di una maggiore efficienza, con una riduzione degli sprechi e dei costi di produzione. Grazie a queste tecnologie e l’enorme quantità di dati raccolta è possibile ottenere informazioni preziose su qualità e risorse impiegate, le quali possono essere utilizzate per migliorare le operazioni e ridurre gli sprechi.
2. Monitoraggio in tempo reale e manutenzione predittiva
L’organizzazione e gestione dei processi produttivi viene facilitata dall’IoT grazie alla raccolta immediata e continua di dati critici relativi a macchinari, attrezzature e agli stessi processi.
Con il monitoraggio in tempo reale, è possibile individuare rapidamente eventuali anomalie o guasti nelle attrezzature. Ciò significa non solo agire prontamente sul problema, ma anche ridurre i tempi di fermo.
Ma non è tutto. Le tecnologie, infatti, oltre a permettere di intervenire tempestivamente su eventuali problemi, consentono anche di prevenirli.
Come già anticipato, uno dei vantaggi dell’implementazione di tecnologie AI e IoT nei processi produttivi è la possibilità di attuare strategie di manutenzione predittiva.
Analizzando i dati dei sensori, è possibile prevedere guasti imminenti e programmare interventi di manutenzione prima ancora che le criticità si presentino.
Oltre alla capacità di prevedere malfunzionamenti e, di conseguenza, il fermo dei macchinari, le nuove tecnologie contribuiscono anche a prolungare la vita delle attrezzature con consistente riduzione dei costi da parte dell’azienda.
3. Miglioramento dell’efficienza produttiva complessiva
L’implementazione delle nuove tecnologie permette di migliorare l’efficienza produttiva complessiva.
- L’implementazione di sensori IoT all’interno delle attrezzature e dei processi di produzione consente la raccolta di un vasto insieme di dati in tempo reale. Dati che vengono poi analizzati dalla AI che utilizza algoritmi avanzati per estrarre informazioni significative e prendere decisioni intelligenti.
- Le aziende possono individuare eventuali inefficienze all’interno del processo produttivo, così come analizzare tendenze passate e attuali per adattare dinamicamente la produzione alle variazioni della richiesta e migliorare la qualità della produzione stessa.
- In ultimo, ma non meno importante, l’analisi dei dati provenienti da sensori IoT consente una gestione più efficiente dei consumi energetici, dando la possibilità all’AI di identificare opportunità per ridurre il consumo di energia senza compromettere le prestazioni produttive.
Le sfide dell’implementazione di AI e IoT nei processi produttivi
Come ogni grande rivoluzione, inevitabilmente anche quella in atto nell’industria manifatturiera presenta delle sfide per le aziende.
- La prima, probabilmente, è una sfida culturale. Se è vero che queste tecnologie offrono un enorme potenziale per migliorare l’efficienza e la qualità nel processo produttivo, lo è anche che l’uomo non viene sostituito, bensì supportato da sistemi AI o IoT. Tale sfida consiste nell’educare e coinvolgere il personale per accettare e abbracciare questi cambiamenti, vedendo le nuove tecnologie come strumenti per liberare le risorse umane da compiti ripetitivi e monotoni che consentono di concentrarsi su attività più rilevanti, creative e strategiche.
- Un’ulteriore sfida, particolarmente rilevante per le piccole e medie imprese in Italia, è la complessità della transizione all’Industria 4.0. L’adozione di queste tecnologie implica investimenti in formazione e acquisizione di competenze specializzate, richiedendo alle aziende di dotarsi di nuovi professionisti che comprendano a fondo le potenzialità di queste tecnologie e di adottare strumenti che siano in grado di facilitare la transizione alla cosiddetta fabbrica intelligente.
TeamSystem Industry 4.0 per la gestione dei processi produttivi
Ogni rivoluzione è costituita da novità che pongono di fronte a nuove sfide, ma anche da strumenti creati appositamente per aiutare le aziende a percorrere questi nuovi sentieri.
È ciò che, ad esempio, si propone di fare TeamSystem Manufacturing, il gestionale per il settore manifatturiero che favorisce e agevola la collaborazione uomo-macchina.
Questo software gestionale consente di avere a disposizione soluzioni all’avanguardia per la gestione ottimizzata dei reparti di lavorazione meccanica, consentendo una perfetta integrazione con gli altri settori aziendali.
In più, consente di migliorare il collegamento macchina-risorsa, grazie alla raccolta automatica dei dati di produzione, garantendo una opportuna comunicazione con il controllore della macchina, nonché la memorizzazione e analisi delle informazioni.
TeamSystem Manufacturing copre l’intero processo produttivo e sostiene ogni tipo di azienda, grande o piccola che sia, in qualsiasi settore di mercato e a qualunque livello di digitalizzazione.
Il software gestionale per il settore manifatturiero, inoltre, risulta anche molto intuitivo e semplice da usare: caratteristica che offre maggiori opportunità di transizione all’industria 4.0 a qualsiasi tipo di azienda.
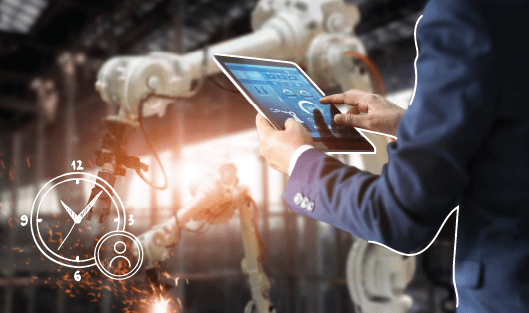