Industria 4.0 cos’è e come sfruttarla
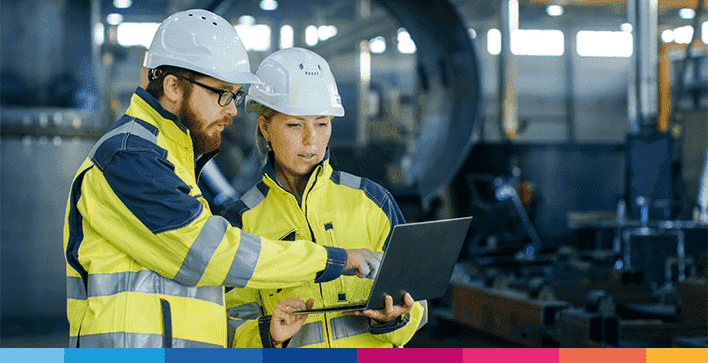
L’Industria 4.0 è il processo che punta ad una produzione industriale completamente automatizzata e interconnessa. Al centro della trasformazione economica in Italia e nel mondo, la sua portata rivoluzionaria è tanto prorompente che gli analisti storico-economici l’hanno già definita Quarta Rivoluzione Industriale.
Vediamo di cosa si tratta nel dettaglio, quali sono le tecnologie e i software industria 4.0 che la stimolano e come si sta evolvendo la situazione in Italia.
Industria 4.0: significato
L’espressione Industria 4.0 è comparsa per la prima volta nel 2011 durante la Fiera di Hannover. Il termine è poi diventato ufficiale due anni dopo, in occasione dello stesso evento, quando un gruppo di lavoro, composto dai principali esponenti delle aziende tedesche di ingegneria ed elettronica, ha presentato un report in cui si analizzavano le principali caratteristiche della quarta rivoluzione industriale e i relativi passaggi da seguire per l’implementazione nella propria fabbrica.
I due postulati principali su cui si basa l’Industria 4.0 sono automazione e interconnessione. Nello specifico questi pilastri si sviluppano su tre diverse aree della gestione aziendale.
La prima riguarda la raccolta e l’analisi dei dati, attraverso tecnologie come IoT, Big Data e Cloud Computing, che hanno l’obiettivo di immagazzinare il maggior numero di informazioni possibili sul funzionamento dei macchinari.
La seconda area interessa l’interazione uomo-macchina: in questo caso intervengono tecnologie come l’IoT, la Realtà Aumentata o Virtuale e il Machine Learning per determinare nuovi livelli di collaborazione tra le macchine e gli operatori, con lo scopo di aumentare l’efficienza del controllo operativo.
L’ultima area di interesse dell’Industria 4.0 è invece la trasformazione di elementi digitali in realtà, attraverso tecnologie come robotica, digital twin e stampa 3D.
I vantaggi del 4.0
L’Industria 4.0 è senz’altro un’opportunità che le aziende devono cogliere per migliorare in termini di crescita, progresso e competitività.
La crescente interconnessione tra macchine, sistemi digitali e operatori rende molto più rapida e corposa l’analisi e la gestione dei dati. Più informazioni si potranno immagazzinare maggiore sarà la velocità nelle scelte operative e nei processi decisionali.
Le aziende che hanno ad oggi adottato sistemi di Industria 4.0 hanno raggiunto i seguenti benefici:
- maggiore efficienza produttiva;
- più flessibilità, sia nella gestione quotidiana dell’operatività sia nello sviluppo di nuove aree di business;
- riduzione dei fermi produttivi. In questo contesto è determinante il ruolo giocato dalla manutenzione predittiva: attraverso la costante analisi dei parametri dei macchinari è possibile, infatti, intuire con anticipo le probabilità di danneggiamento e intervenire prima del guasto;
- risparmio energetico e riduzione degli sprechi;
- maggiore propensione alla customizzazione dei prodotti;
- sostenibilità. Secondo una credenza diffusa ma inesatta, si ritiene che passare all’Industria 4.0 significhi sostituire tutti i propri impianti e/o macchinari, ma non è così. Le soluzioni IoT possono essere implementate direttamente sui macchinari esistenti: con un investimento minimo è possibile intervenire direttamente sulle aree più critiche e ottenere immediati benefici su tutta la struttura operativa.
Industria 4.0: cosa significa per il mercato del lavoro
L’Industria 4.0 sta avendo un forte impatto non solo sull’economia e sul progresso delle fabbriche, ma anche sul mercato del lavoro, che con l’arrivo della quarta rivoluzione industriale sta mutando.
Già nel 2016 la ricerca “The Future of the Jobs“, presentata al World Economic Forum, sottolineava come fattori tecnologici e demografici avrebbero influenzato profondamente l’evoluzione del mercato del lavoro.
Alcune tecnologie, come ad esempio il cloud, e lo smartworking stanno cambiando significativamente le dinamiche del lavoro, snellendo i flussi e aumentando la produttività.
Cambia dunque l’approccio al lavoro e di conseguenza cambiano le competenze richieste ai lavoratori, che diventano più smart e più orientate verso tecnologie e digitalizzazione.
Proprio per favorire questa importante transizione all’interno del mercato del lavoro, il governo ha previsto incentivi per la formazione del personale.
Il credito d’imposta formazione 4.0 è un bonus fiscale erogato, nella misura fino al 50% dei costi sostenuti, alle imprese che attuano percorsi formativi altamente tecnologici a favore dei propri dipendenti.
Industria 4.0: come cambiano le fabbriche
Le fabbriche che vivono l’epoca dell’Industria 4.0 si contraddistinguono per essere altamente tecnologiche ed estremamente interconnesse.
Questo sistema rende le fabbriche 4.0 più flessibili, maggiormente in grado di adattarsi alle necessità interne e a quelle del mercato, e soprattutto in grado di pianificare in modo intelligente il lavoro.
Dunque, investire nella fabbrica 4.0 conviene. E per farlo sono stati stanziati bonus e incentivi che aiutano le aziende a muoversi in questa direzione, come ad esempio il Credito d’imposta per beni strumentali.
Industria 4.0: la situazione in Italia
L’Italia, come tutto l’ecosistema industriale europeo, sta cercando di favorire l’Industria 4.0. Lo sviluppo del 4.0 nel nostro paese inizia nel novembre 2015, quando il Mise, ovvero il Ministero per lo Sviluppo Economico (oggi Ministero delle Imprese e del Made in Italy), annuncia un documento chiamato Industry 4.0, la via italiana per la competitività del manifatturiero.
A partire da quel momento normative, leggi e bonus hanno incentivato crescita e sviluppo verso l’Industria 4.0.
Nel 2016 è stato varato un piano governativo ad hoc che ha poi subito evoluzioni e revisioni: dal Piano Industria 4.0 al Piano Impresa 4.0 fino al Piano Nazionale Transizione 4.0. Durante la pandemia da Covid19 l’Industry 4.0 e le tecnologie ad essa collegate si sono rivelate fondamentali per contrastare la crisi. Nel febbraio 2021 l’allora presidente del Consiglio Mario Draghi ha espresso la necessità di “estendere e rendere facilmente fruibile il Piano Nazionale Transizione 4.0 per accompagnare le imprese nel processo di innovazione tecnologica e di sostenibilità ambientale”.
Le misure prese negli anni a favore della crescita verso l’Industria 4.0 hanno già dato i loro risultati. Basti pensare che il 2022 ha registrato dei dati di crescita molto incoraggianti, come conferma il preconsuntivo del Centro Studi & Cultura di Impresa di Ucimu-sistemi per produrre. La produzione, infatti, è aumentata del 14,6% rispetto al 2021. Anche per questo la domanda italiana di macchinari tecnologici, robot e automazione si è rivelata forte e in crescita, come l’anno precedente.
Quali sono le tecnologie del 4.0?
L’innovazione tecnologica è in costante aggiornamento. Il 4.0 produce soluzioni tecnologiche rivoluzionarie a una velocità impressionante, cercando di migliorare di volta in volta i concetti di automazione e interconnessione.
Per capire quali sono le principali tecnologie dell’Industria 4.0 è possibile rifarsi a uno studio del Boston Consulting Group (BCG), che ha stabilito quali sono, ad oggi, le tecnologie abilitanti del 4.0, necessarie per ogni azienda che vuole affrontare una transizione digitale efficace. Eccole:
- Big Data e Analytics: tutti i sistemi che consentono di raccogliere e riclassificare i dati per ottimizzare i processi operativi e decisionali;
- Simulazione: modelli di simulazione digitale che ottimizzano la produzione reale;
- Sistemi IT: sistemi di gestione informatica che nell’Industria 4.0 sono necessari a tutti i livelli;
- Robot e sistemi automatizzati: tecnologie solitamente implementate sulle macchine per velocizzare l’operatività;
- IoT: sistemi basati sull’Intelligenza Artificiale utili per accelerare i processi di comunicazione uomo-macchina;
- Cloud: soluzioni necessarie per gestire la grande mole di dati 4.0 senza appesantire le strutture IT dell’azienda;
- Realtà aumentata: tecnologie pensate per garantire all’operatore una visione real-time dei processi produttivi;
- Cybersecurity: strutture di sicurezza informatica necessarie a garantire la massima protezione dei sistemi informatizzati su cui si fonda l’Industria 4.0.
Quelle appena citate sono sicuramente le tecnologie cardine dell’Industria 4.0. Un altro elemento tecnologico indispensabile per una gestione efficace della fabbrica 4.0 è sicuramente un software gestionale, in grado di supportare l’azienda a 360° nelle proprie attività.
Gestire la quarta rivoluzione con un software: Industry 4.0
TeamSystem Manufacturing è il software gestionale per il settore manifatturiero che copre l’intero processo della Fabbrica 4.0.
TeamSystem Industry 4.0 affianca l’azienda manifatturiera in tutte le operazioni quotidiane, come ad esempio:
- la pianificazione e schedulazione della produzione,
- la gestione dell’officina;
- il monitoraggio delle macchine utensili.
TeamSystem Manufacturing permette di gestire in modo completo ed efficace ogni aspetto e passaggio della Fabbrica 4.0: la progettazione, la supply chain e l’integrazione IoT nella produzione.
Il software, inoltre, consente di migliorare le performance dell’intera area produttiva, perché semplifica la gestione operativa, supporta nell’ottimizzazione di risorse e materiali, aumenta la produttività e la redditività e riduce al minimo il time to market.
Grazie alla sua tecnologia all’avanguardia, TeamSystem Manufacturing è la soluzione perfetta per una pianificazione efficace della produzione che permette di migliorare le performance aziendali e restare sempre competitivi.
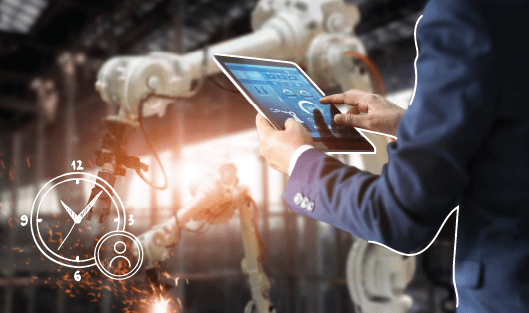